High Functionality
BLE Series models have been fully revamped. The motor, driver, and cable have been redesigned. While retaining the original advantages of the brushless DC motors. This makes the BLE2 Series easy to use and highly functional. This advanced model reveals its excellence with every application.
NexBL is the new brushless motor from China Motor. All of the structures have been updated, with a focus on maximizing the performance demanded of a motor. A combination of unprecedented compactness, high power, and high efficiency has been realized.
EASY Setting
Overhauling the motor structure has made it even more compact, as well as increasing the power and efficiency. The driver comes with a digital indication panel, that easily allows speed to be set via a single potentiometer. Additionally, connection cables now come with the option to choose the pull-out direction and a max. distance of 20 m can be secured via direct connection.
BLE2 Series embodies what the customers find easy to use.
The Control Panel allows for easy setting.
A control panel is installed on the front face of the drive. Operating data and parameters can be set via operation key and setting dial, whilst looking at the digital display.
Quick and Accurate Wiring and Connection
Use of a spring-type connector allows for quick and accurate wiring.
Water resistance in compliance with IEC 60529 and IEC 60034-5
A new type of connector has been designed, which includes a built-in Gasket and O-ring. This allows for the motor to achieve an IP66 degree of protection in both the motor and connector, enabling it to be used in an environment where powerful water jets may be an issue. Additionally the connectors lock lever does not require a screw fitting, which allows for easy connection.
*The driver portion is IP20.
Connector Structure
Installation Method
Standardized Use of Stainless
EURONORM X 10 CrNiS 18 9 stainless steel is used for the shaft, which has excellent anti-corrosive properties. Stainless steel is also used in parallel keys and installation screws.
Easy Assembly with a Combination Type
With cutting-processed boss section and installation surface, the installation precision between the device and gearhead has been improved. This improved machining as also resulted in a quiter product. Furthermore, as the combination type of the motor and gearhead comes pre-assembled, it is fast and simple to directly couple onto a device.
Selectable Pull-out Direction and Directly Connectable Cables
Two types of connection cables are available based on the desired pull-out direction. Since one connection cable can be used to connect the motor and the driver directly, with a maximum distance of 20 m, there is no need for special connectors.
Selectable Cable Pull-out Direction
Pull-out on output shaft side / Pull-out on rear of the motor
Connection with one Connection Cable,
No need for Relays
Because only one cable is required for the power line, signal line, and ground wire, wiring process can be reduced.
Effective Utilization of Installation Space
This new driver has a compact and slim body through optimal layout of its internal parts. Multiple drivers can now be installed in contact with each other, making it possible to reduce the amount of installation space or increase the number of axes within the same equipment space.
Compact, Slim-Body Driver
Installation Area 64 cm2
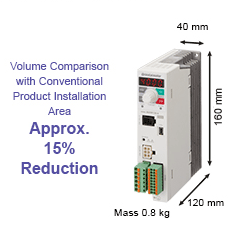
Side-by-Side Installation of
Multiple Drivers
Conventional BLE Series Drivers
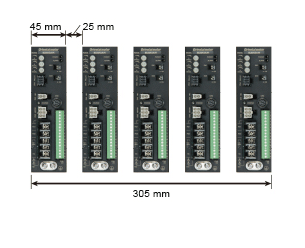
BLE2 Series Drivers
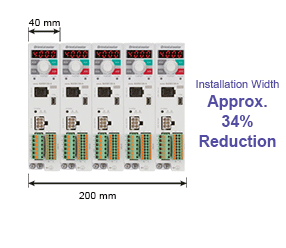
WIDE Speed Control Range
Brushless DC motors are without brushes, which is a major drawback of brushed DC motors, this allows for quieter and maintenance free operation. Because the BLE2 Series has a permanent magnet it allows for a compact design with high power and high efficiency.
Wide Speed Control Range
Brushless motors have a wider range of speed control than AC motors. Additionally they are ideal for applications that require a constant torque from low to high speed.
Example:
Product Group |
Speed Control Range✽ |
Speed Ratio |
Brushless Motors BLE2 Series |
80∼4000 r/min |
1:50 |
Inverter-Controlled Three-Phase Induction Motor |
200∼2400 r/min |
1:12 |
AC Speed Control Motors |
50 Hz : 90∼1400 r/min 60 Hz : 90∼1600 r/min |
1:15 1:17 |
✽Speed control range varies from model to model.
Stable Speed Control
Brushless motors constantly monitors feedback signals from the motor and adjusts the applied voltage by comparing them against the set speed. This allows the motor to rotate at a stable speed from low to high speeds even when the load fluctuates.
Comparison of Speed Variation (Reference value)
Slim, Light, High Power
Brushless motors are slim, light and high power because permanent magnets are used in the rotor portion. It contributes to the downsizing of equipment.
Showing the space saving potential
Saves Energy
Brushless motors significantly reduce power consumption as the use of permanent magnets in the rotor portion prevents secondary loss from the rotor. Among other improvements, this helps the equipment to save energy.
Energy Saving potential illustrated
✽at net frequency 50 Hz
ENHANCED Control Possibilities
Features four data setting methods and various functions that are customisable. By using data setting software, equipment start-up and checking operating status is simple. China Motors offers functions that meet the customers' needs and situations.
Operating Method
• Local Control Operating: Set via the front control panel. It can be used for test operation.
• Remote Control Operation: Set via external signals and data setting software MEXE02.
Control Panel on the Driver
External Speed
Potentiometer PAVR2-20K
External DC Voltage
Data Setting Software
MEXE02*
Setting Possibilities
Setting Contents |
Applications and Purposes |
Setting Value |
Setting Method |
Control Panel |
External Speed Potentiometer PAVR2-20K |
External DC Voltage |
Data Setting Software MEXE02 |
Speed |
For operating at an arbitrary speed. |
80∼4000 r/min |
● |
● |
● |
● |
Torque Limiting |
For suppressing the motor's max. output power for safety purpose or limiting it depending on the load. |
0∼300% |
● |
● |
● |
● |
Acceleration/Deceleration Time |
For setting the acceleration time and deceleration time to prevent impact to the load when starting and stopping. |
0∼15.0 seconds |
● |
- |
- |
● |
Multistep Speed-Change Operation |
For operating at more than 2 speeds. |
Max. 16 speeds |
● |
- |
- |
● |
Parallel-Motor Operation |
For operating multiple motors at the same speed. |
20 units max. (When using a potentiometer) |
- |
● |
● |
- |